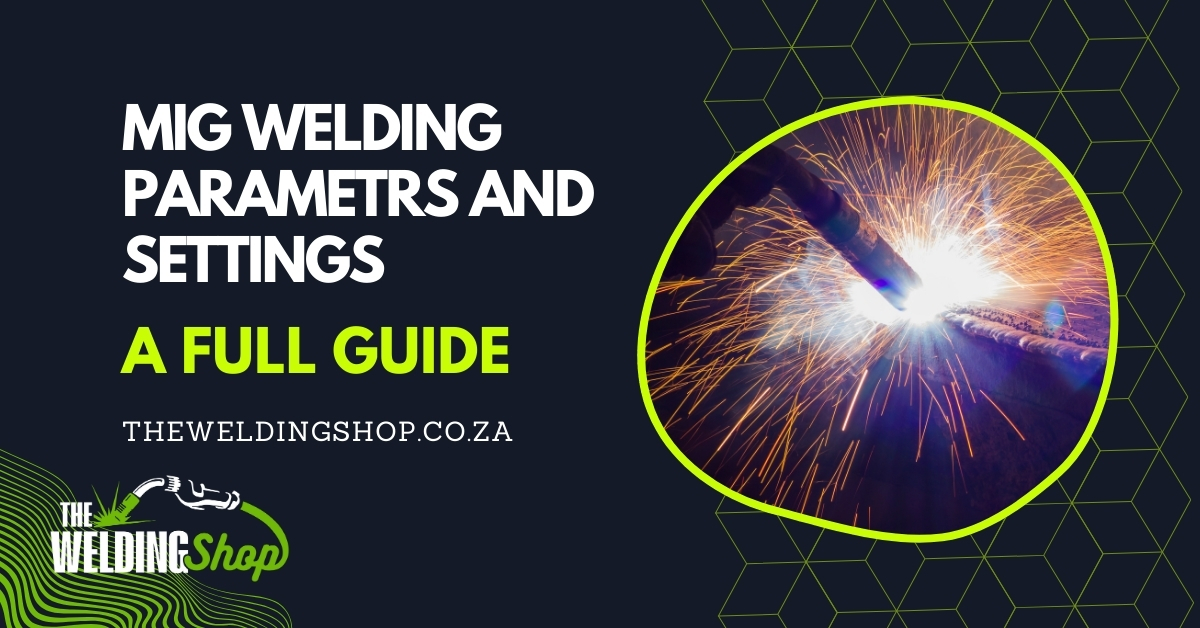
MIG Welding Parameters and Settings Explained: How to Optimize Parameters for Stronger, Cleaner Welds
MIG welding parametsr and settings for beginners, MIG welding parameter chart, best MIG welding settings for steel, how to set MIG welding parameters, MIG welding voltage and wire speed settings, MIG welding troubleshooting settings, MIG welding settings for aluminum, optimizing MIG welding parameters, MIG welding gas pressure settings, MIG welding amperage and voltage guide.
MIG welding, or Metal Inert Gas welding, is one of the most popular welding techniques due to its versatility, speed, and ease of use. However, achieving flawless welds requires a deep understanding of MIG welding parameters and settings. Whether you’re a beginner or an experienced welder, this guide will walk you through everything you need to know to optimise your MIG welding process for stronger, cleaner, and more efficient results.
Understanding MIG Welding Parameters
MIG welding parameters are the variables that determine the quality and characteristics of your weld. These include voltage, wire feed speed, amperage, shielding gas, and electrode stick-out. Getting these settings right is crucial for achieving the desired weld penetration, bead appearance, and overall strength.
Why Are MIG Welding Parameters Important?
- Weld Quality: Proper settings ensure strong, consistent welds with minimal defects like porosity or spatter.
- Efficiency: Optimised parameters reduce waste and save time.
- Material Compatibility: Different materials and thicknesses require specific settings for optimal results.
Key MIG Welding Parameters and Settings
1. Voltage
Voltage controls the arc length and heat input. Too high, and you risk burning through the material; too low, and the weld may lack penetration.
- Low Voltage: Produces a shorter arc, ideal for thin materials.
- High Voltage: Creates a longer arc, better suited for thicker materials.
2. Wire Feed Speed
Wire feed speed determines how much filler metal is deposited into the weld pool. It directly affects amperage and weld bead size.
- Faster Speed: Increases amperage and weld size.
- Slower Speed: Reduces amperage and creates a smaller bead.
3. Amperage
Amperage influences the heat and penetration of the weld. It’s determined by the wire feed speed and voltage settings.
- Higher Amperage: Better for thicker materials.
- Lower Amperage: Ideal for thin or delicate materials.
4. Shielding Gas
Shielding gas protects the weld pool from contamination. Common gases include:
- 100% CO2: Affordable and good for deep penetration.
- 75% Argon + 25% CO2: Balanced for most materials.
- 100% Argon: Best for aluminium and non-ferrous metals.
5. Electrode Stick-Out
This is the distance between the contact tip and the workpiece. A typical stick-out is 6 to 10 mm.
- Too Short: Can cause overheating and spatter.
- Too Long: Leads to poor arc stability and inconsistent welds.
MIG Welding Parameter Setting for Mild Steel
Step 1: Determine your workpiece thickness.
Use the chart below to find the starting point for your welding project.
Mild Steel Gas Welding Parameters
Material Thickness (mm) | Wire Diameter (mm) | Voltage (V) | Current (A) |
---|---|---|---|
0.5 | 0.6 | 15–17 | 20–30 |
1.0 | 0.6 – 0.8 | 16–18 | 30–40 |
1.5 | 0.6 – 0.8 | 17–19 | 35–50 |
2.0 | 0.8 – 1.0 | 18–20 | 40–90 |
2.5 | 0.8 – 1.0 | 19–21 | 50–100 |
3.0 | 0.8 – 1.2 | 20–22 | 90–120 |
3.5 | 0.8 – 1.2 | 21–23 | 100–130 |
4.0 | 0.8 – 1.2 | 22–24 | 120–150 |
4.5 | 0.8 – 1.2 | 23–25 | 140–170 |
5.0 | 0.8 – 1.2 | 24–26 | 150–180 |
5.5 | 0.8 – 1.2 | 25–27 | 160–190 |
6.0 | 0.8 – 1.2 | 26–28 | 180–210 |
Mild Steel Gasless Welding Parameter Settings
Gasless Flux Core Welding Parameters
Recommended for materials 1.6 mm and thicker.
Material Thickness (mm) | Amp Range | Voltage |
---|---|---|
1.000 | 70 A | 13 V |
1.500 | 85 A | 16.5 V |
2.000 | 110 A | 18.5 V |
2.500 | 120 A | 19 V |
3.000 | 150 A | 20.5 V |
4.000 | 160 A | 21.5 V |
Then fine tune your amperage and voltage settings accordingly until you reach the required weld.
Common MIG Welding Mistakes & How to Fix Them
1. Excessive Spatter
- Cause: Incorrect voltage or wire feed speed.
- Fix: Adjust voltage and wire speed settings. Ensure the workpiece is clean.
2. Porosity
- Cause: Contaminated shielding gas or dirty workpiece.
- Fix: Check gas flow rate and clean the material thoroughly.
3. Poor Penetration
- Cause: Low voltage or amperage.
- Fix: Increase voltage and wire feed speed.
4. Burn-Through
- Cause: Excessive heat input.
- Fix: Reduce voltage and wire speed, or increase travel speed.
Essential Safety Tips for MIG Welders
- Wear Protective Gear: Always use a welding helmet, gloves, and flame-resistant clothing.
- Ensure Proper Ventilation: Welding fumes can be hazardous.
- Inspect Equipment: Regularly check your welding machine, cables, and gas supply for damage.
- Follow Manufacturer Guidelines: Adhere to the recommended settings for your specific machine.
MIG Welding Parameter Charts & Tools
Using a MIG welding parameter chart can simplify the process of finding the right settings for your project. These charts provide recommended voltage, wire speed, and gas flow rates based on material type and thickness. Many modern MIG welders also come with built-in calculators or apps to help you dial in the perfect settings.
Understanding Synergic MIG Welders
Most single-phase MIG welders are synergic welders, meaning the amperage and wire feed speed are controlled in synergy with each other. This simplifies the setup process, as the machine automatically adjusts the wire speed based on the voltage setting. However, this also means there is no separate wire speed controller on single-phase machines.
On the other hand, three-phase MIG welders typically include a separate wire speed controller, giving welders more precise control over their settings. This is particularly useful for advanced applications or when working with a wide range of materials and thicknesses.
Conclusion: Perfect Your MIG Welding Skills
Mastering MIG welding parameters and settings is the key to achieving strong, clean, and efficient welds. By understanding the relationship between voltage, wire feed speed, amperage, and shielding gas, you can tackle any welding project with confidence. Remember, practice makes perfect—so don’t be afraid to experiment and fine-tune your settings.
Ready to take your welding to the next level? Explore our range of top-rated MIG welders and accessories at The Welding Shop to find the perfect tools for your needs. Have questions or tips to share? Leave a comment below—we’d love to hear from you!